The Art of Guilloche
A Comprehensive Guide to Understanding and Appreciating Watch Dial Craftsmanship
I. Introduction
In the world of haute horlogerie, few decorative techniques capture the imagination quite like guilloche. This centuries-old art of engraving intricate, repetitive patterns on watch dials and movements has long been a hallmark of fine watchmaking, elevating timepieces from mere instruments to miniature works of art.
Guilloche, pronounced “gee-oh-shay,” is derived from the French term “guillocher,” meaning to decorate with intersecting curved lines. This technique transforms plain surfaces into mesmerizing displays of geometry and light, adding depth, texture, and character to watch dials.
Beyond its undeniable aesthetic appeal, guilloche serves practical purposes in watchmaking. The engraved patterns reduce glare on the dial, enhancing legibility in various lighting conditions. Additionally, the technique can help disguise minor imperfections and protect the dial surface from scratches and wear over time.
As we embark on this exploration of guilloche, we’ll uncover its rich history, delve into the techniques used to create these stunning patterns, learn how to recognize quality craftsmanship, and discover why this art form continues to captivate watch enthusiasts and collectors around the world.
II. The History of Guilloche
The roots of guilloche can be traced back to the 16th century, originating not in watchmaking, but in woodworking and metalworking. The earliest known example of a guilloched watch case dates to 1624, created by the French watchmaker Jean Vallier.
However, it was in the 18th and 19th centuries that guilloche truly flourished. The technique gained immense popularity during this period, coinciding with the rise of the Industrial Revolution and advancements in machining technology.
One of the most famous applications of guilloche outside of watchmaking was in the creation of Fabergé eggs. These opulent objets d’art, created for the Russian Imperial family, often featured exquisite guilloche enamel work, showcasing the technique’s versatility and prestige.
In the world of horology, Abraham-Louis Breguet is credited with popularizing guilloche on watch dials. Breguet began using the technique in 1786, recognizing its potential to enhance both the aesthetics and functionality of his timepieces. His distinctive style, characterized by eccentric engine-turned patterns, became a signature of the brand that continues to this day.
As watchmaking evolved through the 19th and 20th centuries, guilloche remained a mark of high-end craftsmanship. However, the advent of mass production and changing design trends led to a decline in its use by the mid-20th century.
Fortunately, the mechanical watch renaissance of the 1980s and beyond brought renewed interest in traditional watchmaking crafts, including guilloche. Today, both established luxury brands and independent watchmakers continue to push the boundaries of this art form, blending time-honored techniques with modern innovations.
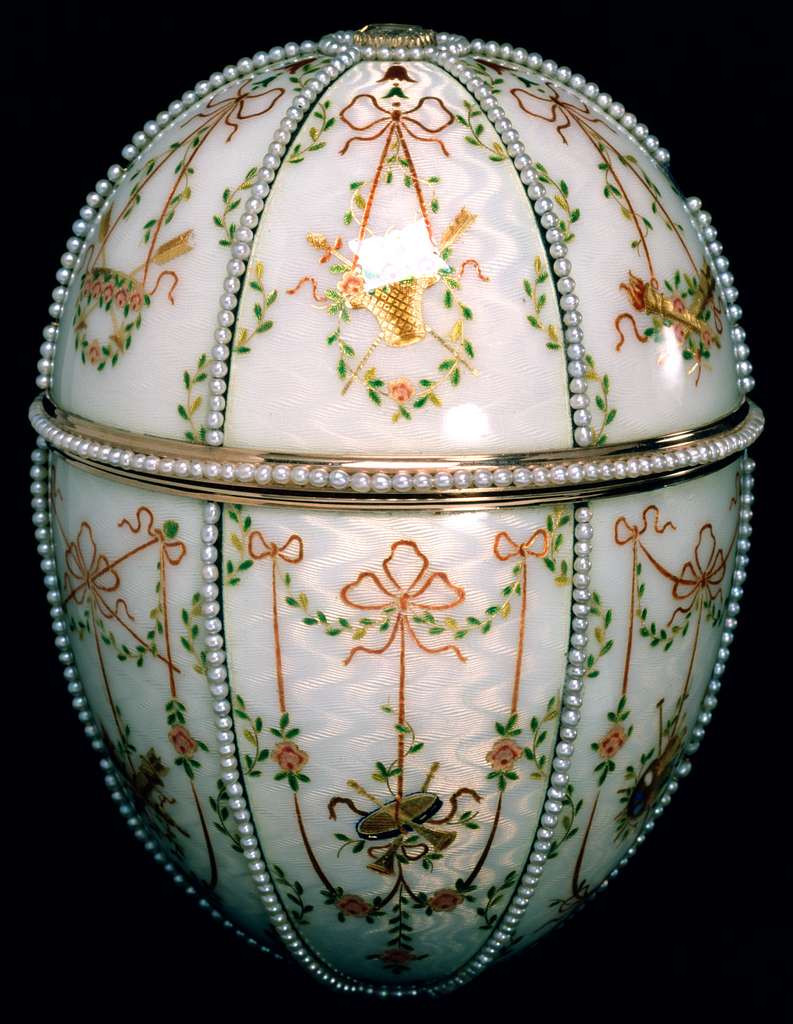
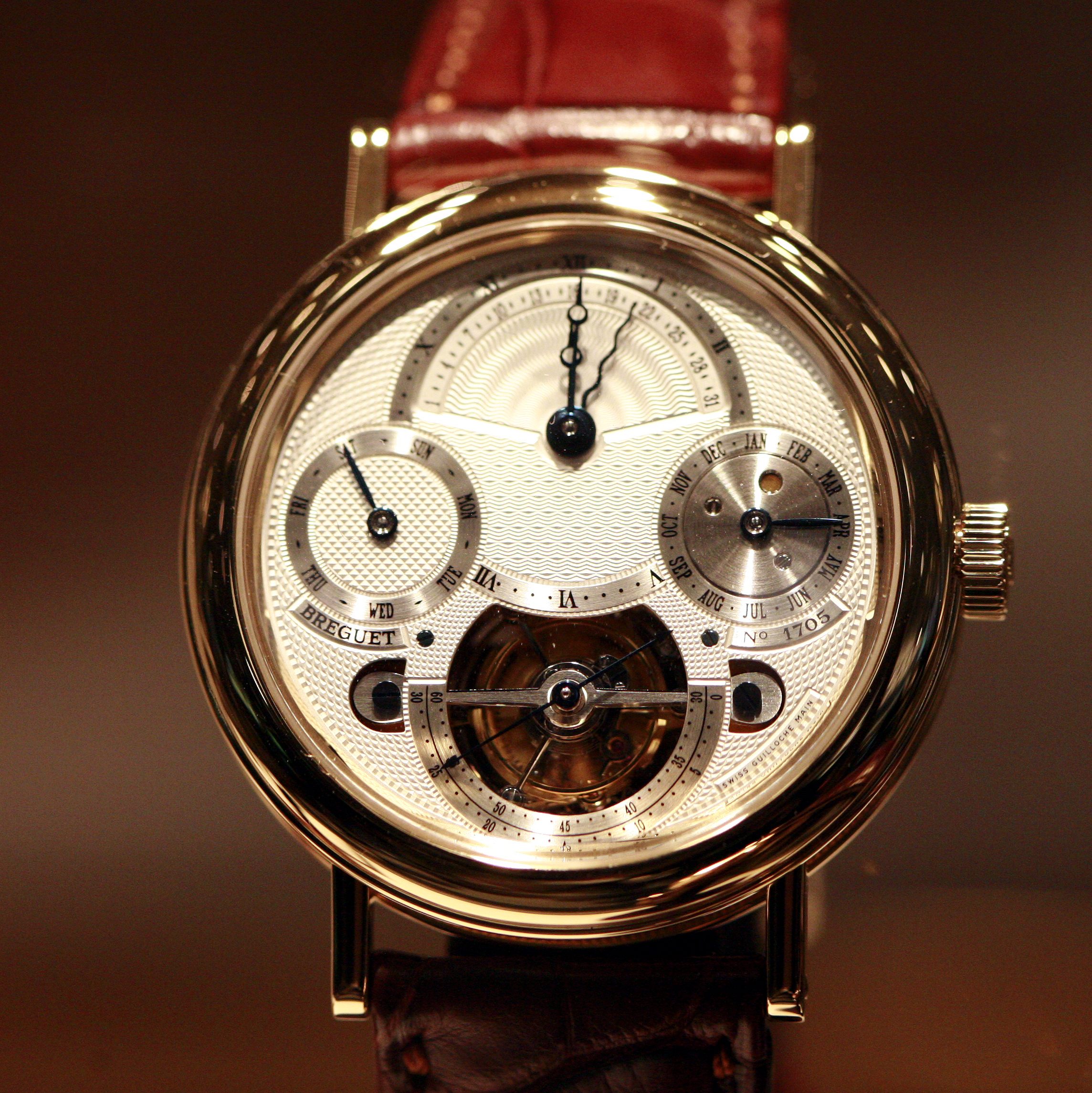
III. Guilloche Techniques
The creation of guilloche patterns involves specialized equipment and considerable skill. There are several methods used to produce these intricate designs, each with its own characteristics:
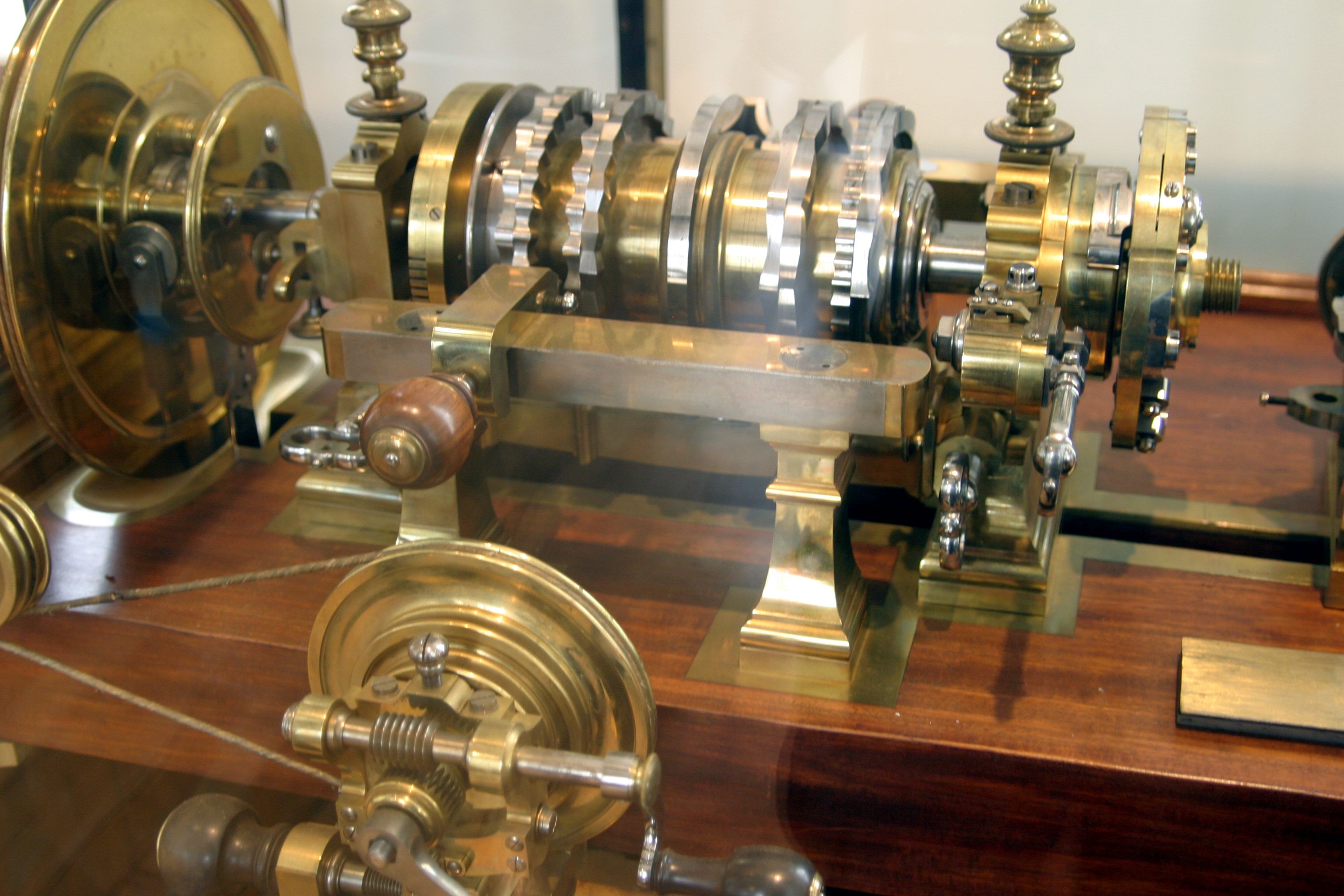
Traditional Methods
Rose Engine: The rose engine is the primary tool for creating circular and oval guilloche patterns. It consists of a headstock that rocks back and forth as the workpiece rotates, guided by interchangeable rosettes (cam-like pattern guides).
Straight-Line Machine: As the name suggests, this machine is used for creating straight-line patterns. It moves the workpiece in a linear fashion while the cutting tool engraves the surface.
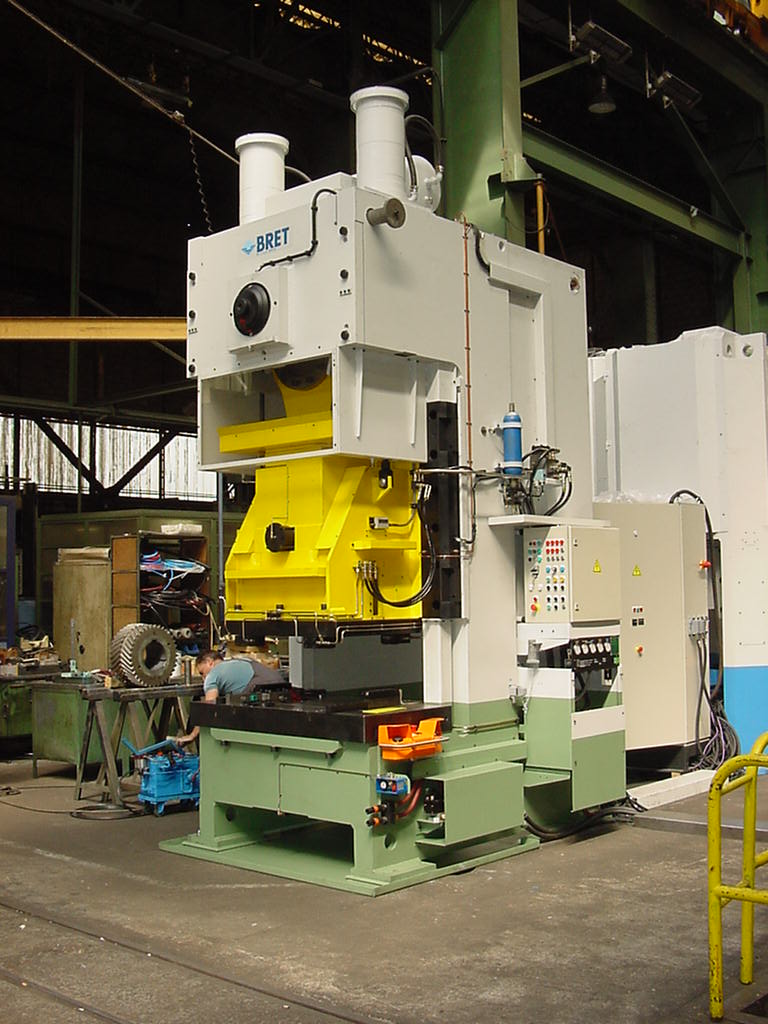
Modern Methods
CNC Machining: Computer Numerical Control (CNC) machines can replicate guilloche patterns with high precision and consistency. These machines are programmed to follow complex paths, creating intricate designs quickly and accurately.
Embossed Dials: This method uses a stamping process to create guilloche-like patterns. A master stamp, often created using CNC technology, is pressed into the dial material to produce the design.
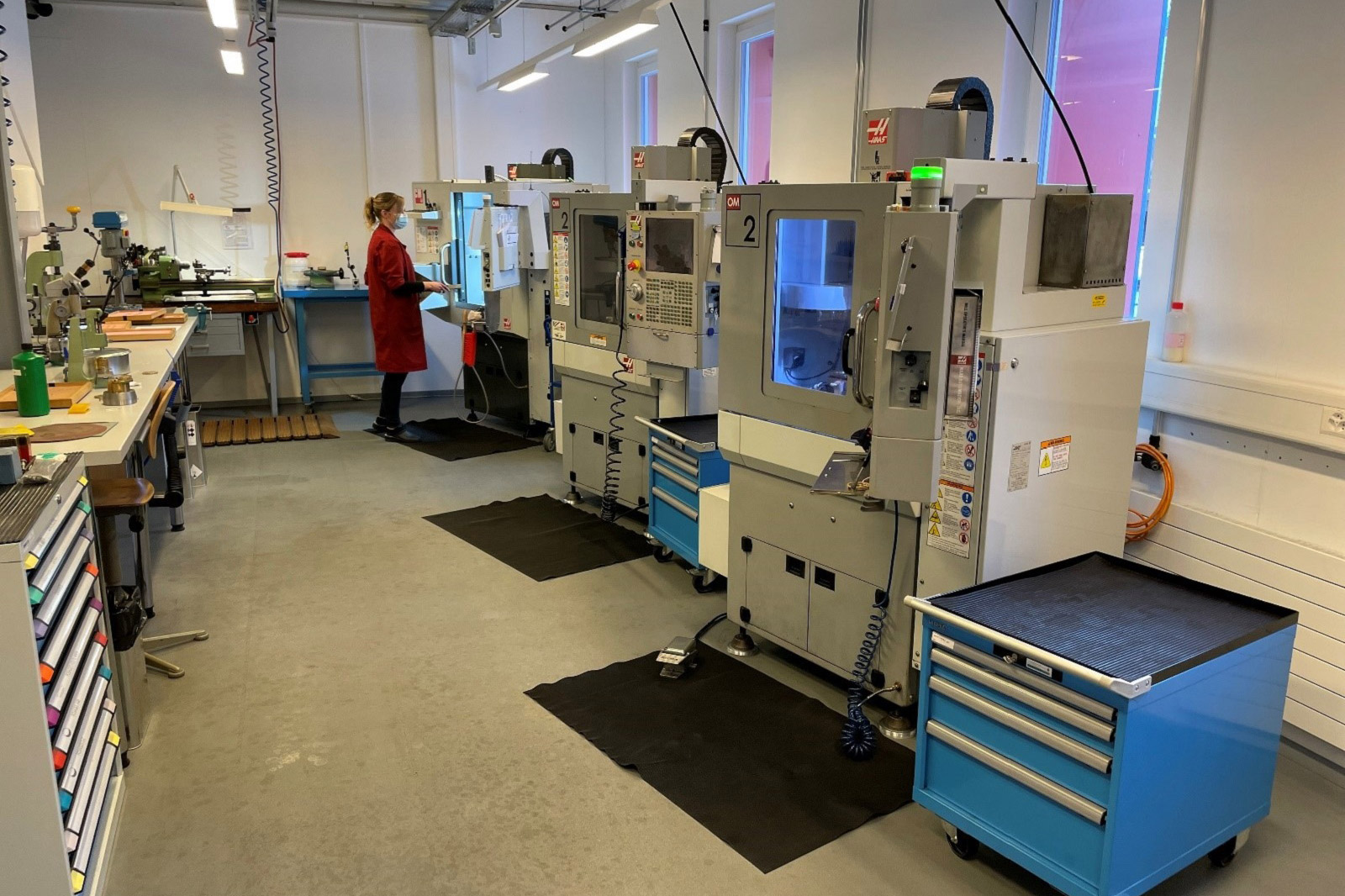
Comparison of Techniques
Each method has its advantages and characteristics:
1 – Traditional hand-operated machines offer a unique, artisanal quality. The subtle imperfections and variations in hand-engraved guilloche are praised by collectors and enthusiasts.
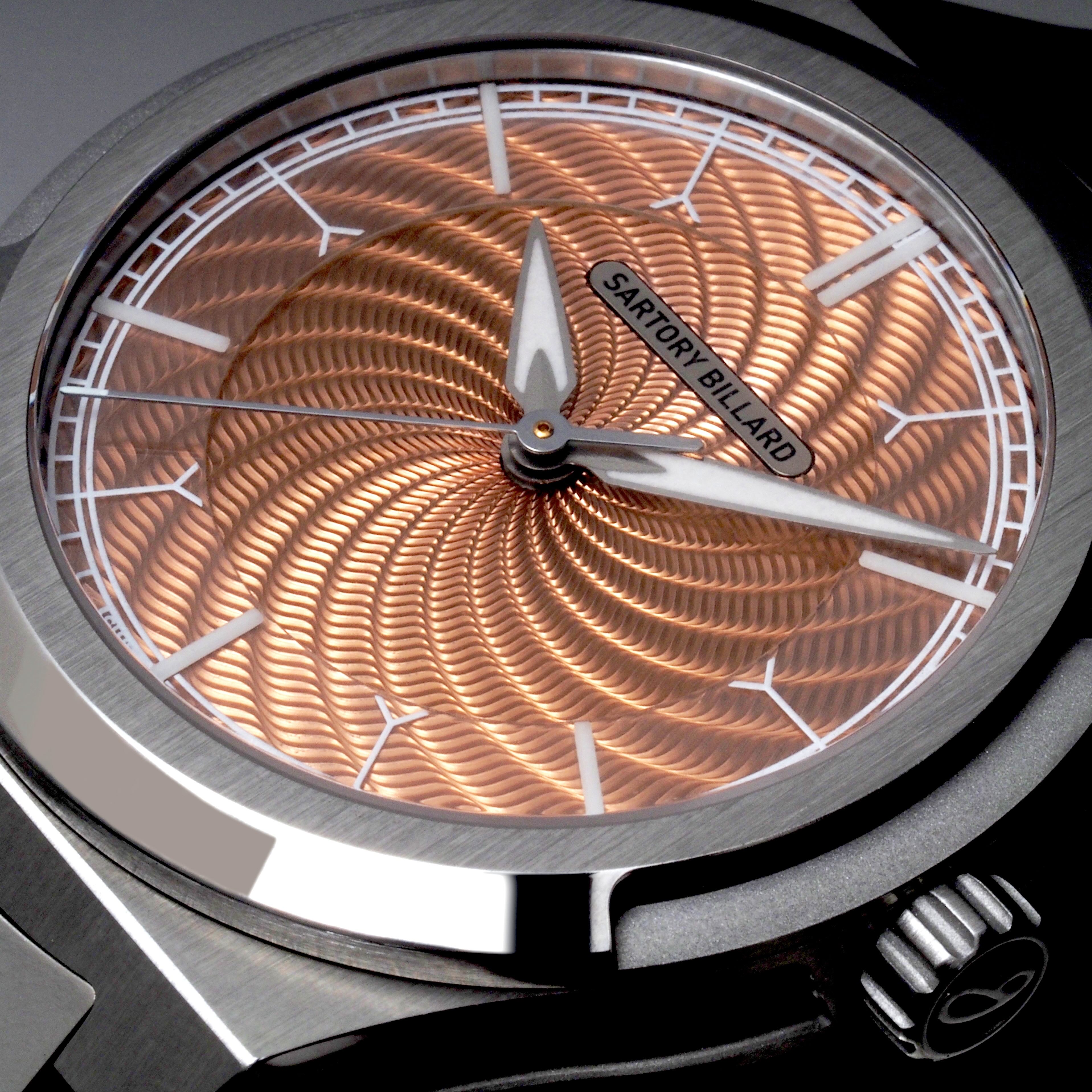
2 – CNC machining provides exceptional precision and consistency, allowing for complex patterns that would be challenging to produce by hand. Technique, tools and setup are crucial to achieve good results.
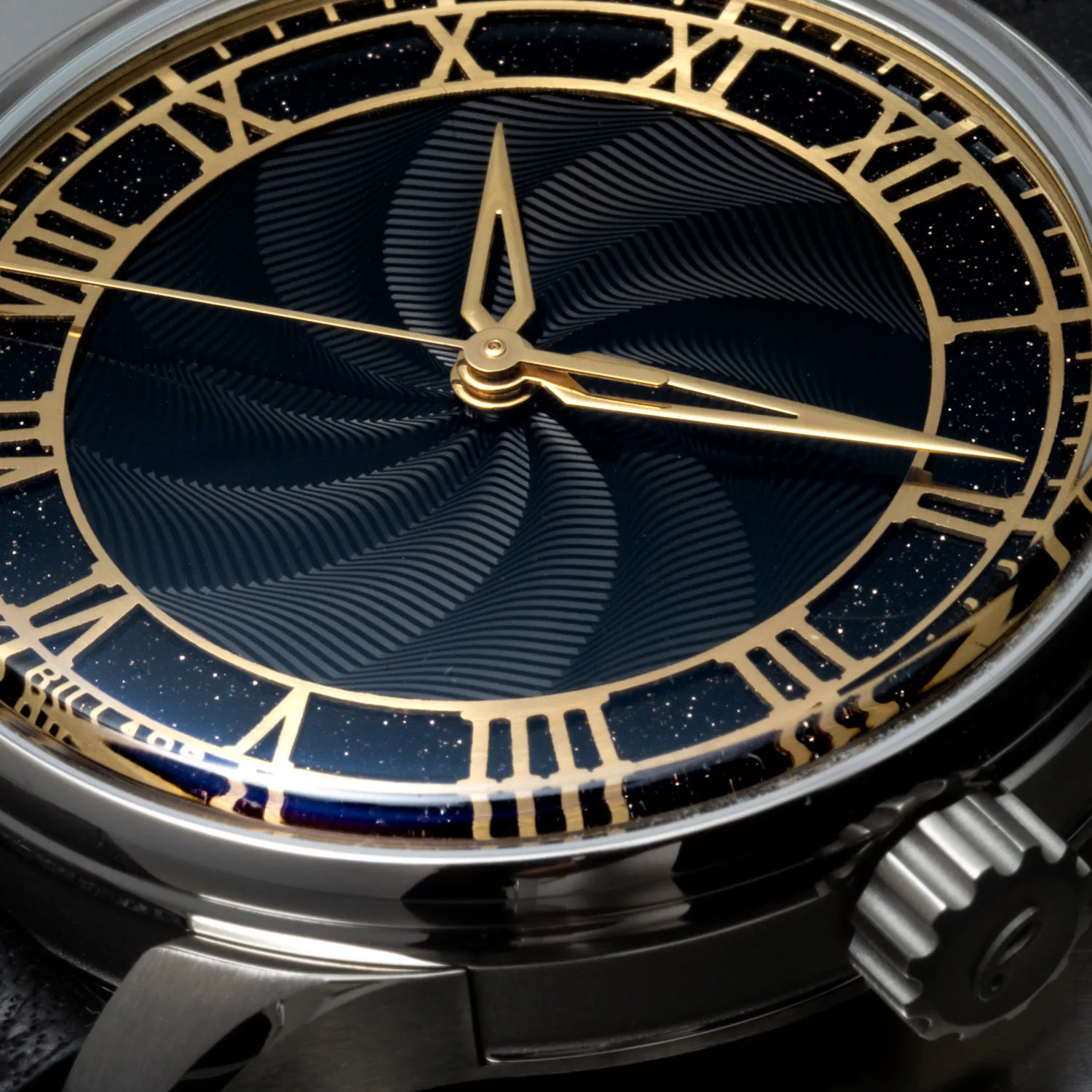
3 – Embossed dials offer a cost-effective way to achieve a guilloche-like appearance, but typically lack the depth and sharpness of true engraved guilloche. Usually will be present on value oriented watches.
IV. Recognizing Quality Guilloche
The ability to discern high-quality guilloche work is a valuable skill for any watch enthusiast or collector. Whether examining a vintage timepiece or considering a modern luxury watch, understanding the hallmarks of superior guilloche can enhance your appreciation and inform your choices.
A. Key Factors to Consider
1 – Precision and Consistency:
High-quality guilloche exhibits uniform patterns with evenly spaced, consistently deep lines. The regularity of the pattern should be maintained across the entire decorated surface.
2- Depth and Sharpness:
Superior guilloche work features crisp, well-defined lines that create a noticeable play of light and shadow. The engraving should have a discernible depth, giving the pattern a three-dimensional quality.
3 – Alignment and Symmetry:
In complex designs, different sections of the pattern should align perfectly where they meet. Circular patterns should be concentric and properly centered on the dial.
4 – Overall Finish and Lustre:
The engraved surface should have a smooth, polished appearance. Light should reflect evenly across the pattern, creating a subtle shimmer as the watch moves.
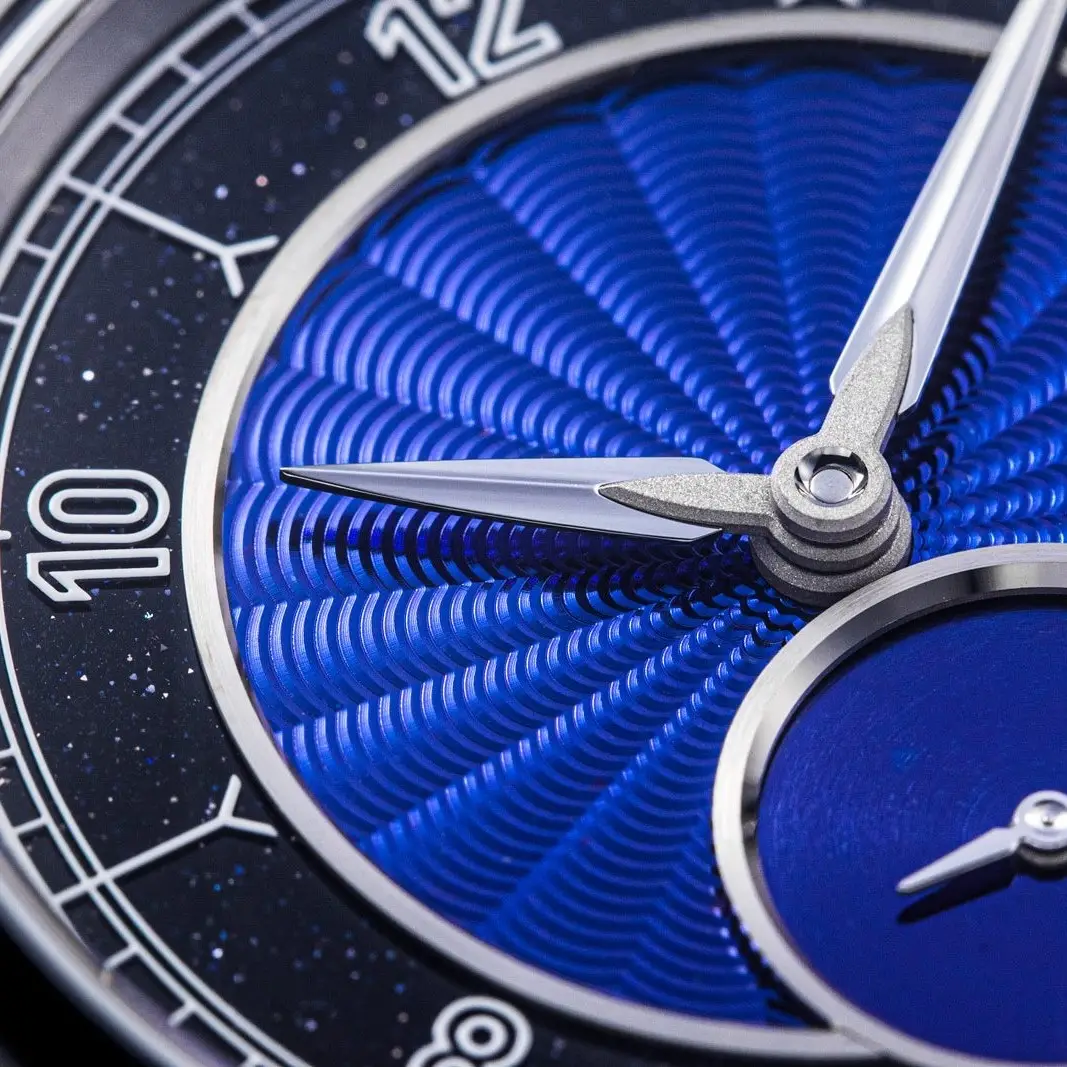
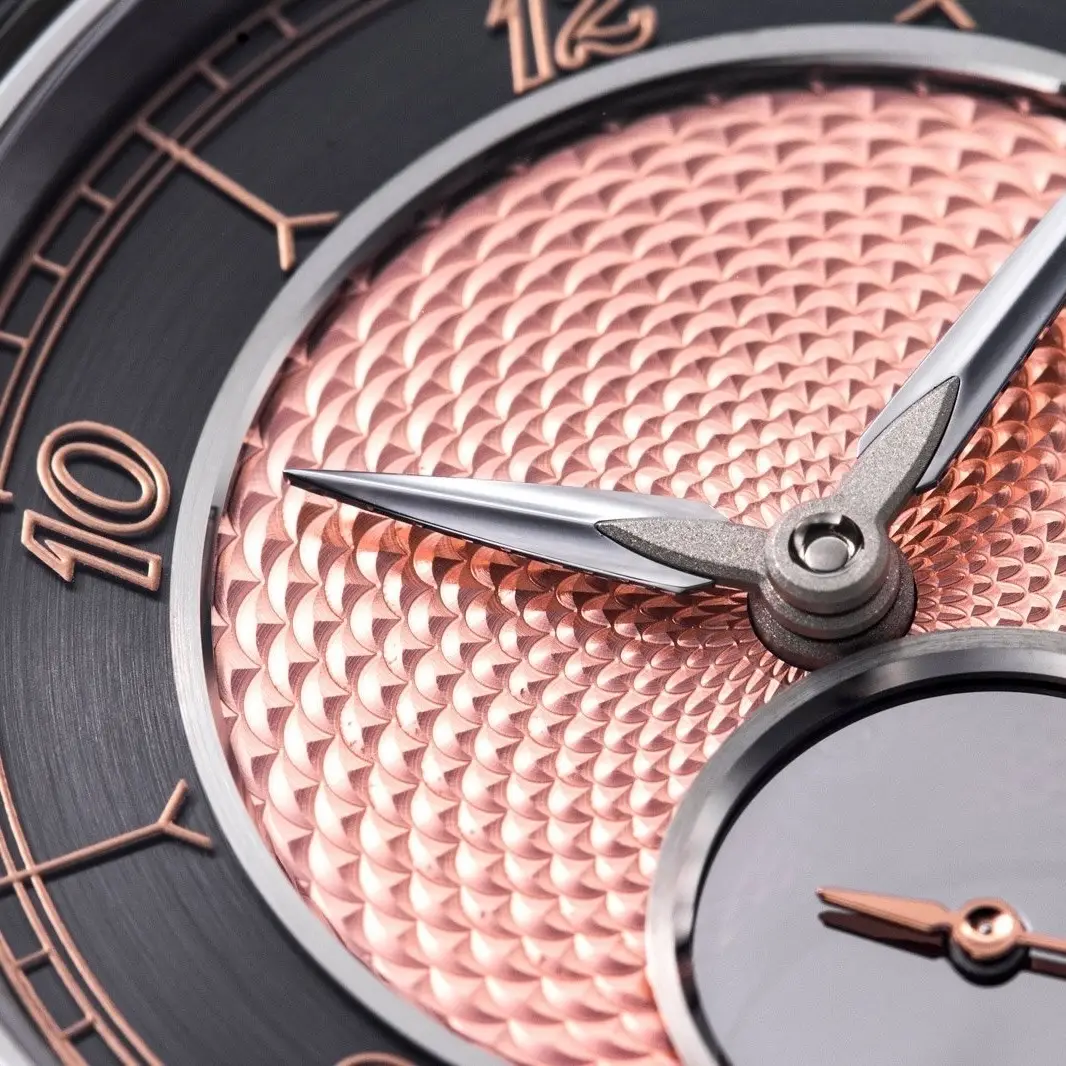
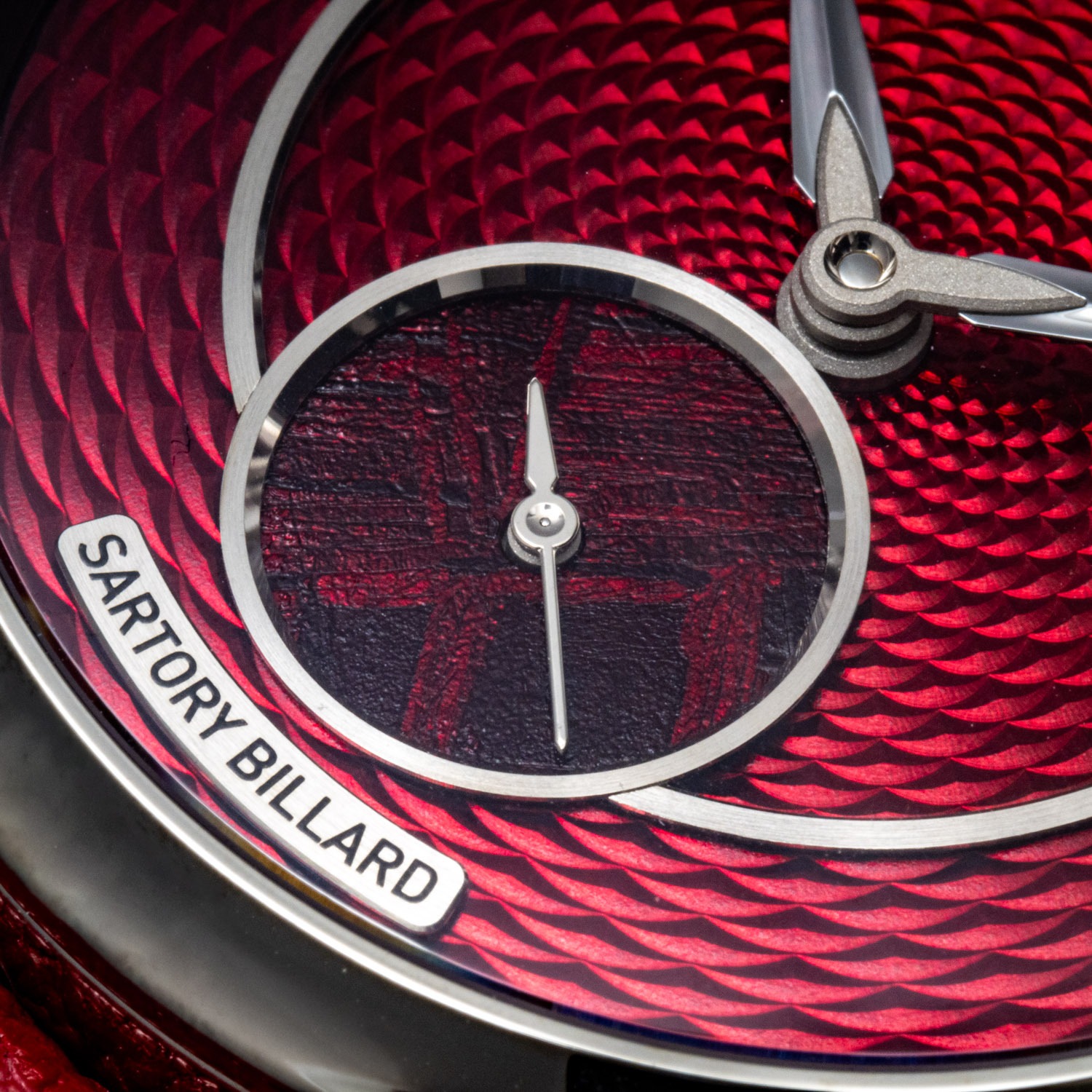
B. Common Issues
Even renowned watchmakers occasionally produce less-than-perfect guilloche. Familiarizing yourself with common issues can sharpen your eye for quality. Here are some problems to watch for, along with their colloquial names in the industry:
☉ « Wobble »: Wavering lines instead of straight ones, often due to instability in the engraving process or improperly secured workpiece.
☉ « Depth Variance »: Inconsistent engraving depth across the pattern, resulting in uneven light reflection.
☉ « Spacing Drift »: Uneven spacing between lines, disrupting the pattern’s uniformity.
☉ « Pattern Mismatch »: Misalignment where different sections of the pattern meet, often seen in complex designs.
☉ « Edge Burr »: Rough edges along the engraved lines, indicating poor tool control or inadequate finishing.
☉ « Off-Center »: Patterns that aren’t properly centered on the dial, particularly noticeable with circular designs.
☉ « Pattern Stretch »: Distorted or unnaturally stretched patterns, often seen near the edges of a dial.
☉ « Stray Marks »: Unintended tool marks or scratches outside the intended pattern.
☉ « Fade Out »: Incomplete or faded sections of the pattern, typically near edges or in tight corners.
By familiarizing yourself with these factors and potential issues, you’ll be better equipped to assess the quality of guilloche work on watch dials. Remember, while perfection is the goal, the charm of hand-engraved guilloche often lies in its subtle irregularities – a testament to the human touch behind this intricate art form.
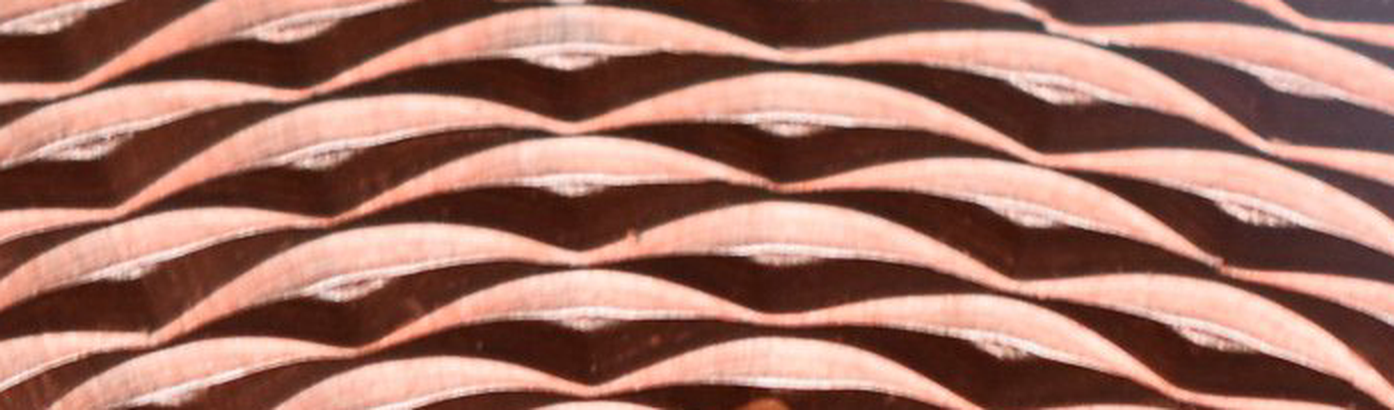
V. Hand-Engraved vs. Machine-Made Guilloche
In the world of haute horlogerie, the debate between hand-crafted and machine-made elements is ongoing. This discussion is particularly relevant when it comes to guilloche, where both traditional hand-engraving and modern CNC techniques can produce stunning results. Understanding the differences between these methods can enhance your appreciation of the craft and inform your collecting decisions.
A. Characteristics of Hand-Engraved Work
Hand-engraved guilloche, created using traditional rose engines or straight-line machines, possesses several distinctive qualities:
☉ Subtle Imperfections: The human touch introduces minor variations in line depth, spacing, and alignment.
☉ Artistic Interpretation: Each artisan brings their own style to the work. Even when following a set pattern, there’s room for individual interpretation in the execution.
☉ Limited Production: Due to the time-intensive nature of hand-engraving, these pieces are often produced in smaller numbers, adding to their exclusivity.
B. Characteristics of Machine-Made Work
Hand-engraved guilloche, created using traditional rose engines or straight-line machines, possesses several distinctive qualities:
☉ CNC (Computer Numerical Control) machining has revolutionized many aspects of watchmaking, including guilloche production:
☉ Precision and Consistency: Machine-made guilloche exhibits exceptional uniformity. Patterns are replicated with exact precision across the dial.
☉ Complex Designs: CNC machines can execute intricate patterns that would be extremely challenging or impossible to create by hand.
☉ Efficiency: Machine-made guilloche can be produced more quickly and in larger quantities, making it more accessible in mid-range luxury watches.
☉ Perfect Symmetry: Circular patterns are perfectly concentric, and intersecting patterns align with flawless accuracy.
C. The Value of Craftsmanship Over Method
While the debate between hand-engraved and machine-made guilloche continues, it’s crucial to recognize that the true value lies in the end result rather than the method itself. If an artist or machinist can produce a guilloche dial of exceptional quality, there is no inherent benefit to hand-engraved guilloche over machine-made versions.
The key factors in evaluating guilloche work should always be:
- The overall quality and precision of the pattern
- The depth and consistency of the engraving
- The visual impact and aesthetic appeal of the final product
In many cases, modern CNC machining can produce guilloche work that is indistinguishable from hand-engraved pieces, even to trained eyes. The most important aspect is the skill and artistry behind the design and execution, regardless of the specific technique used.
Ultimately, the value of a guilloche dial should be judged on its beauty, craftsmanship, and how well it complements the overall watch design, rather than solely on whether it was created by hand or machine.
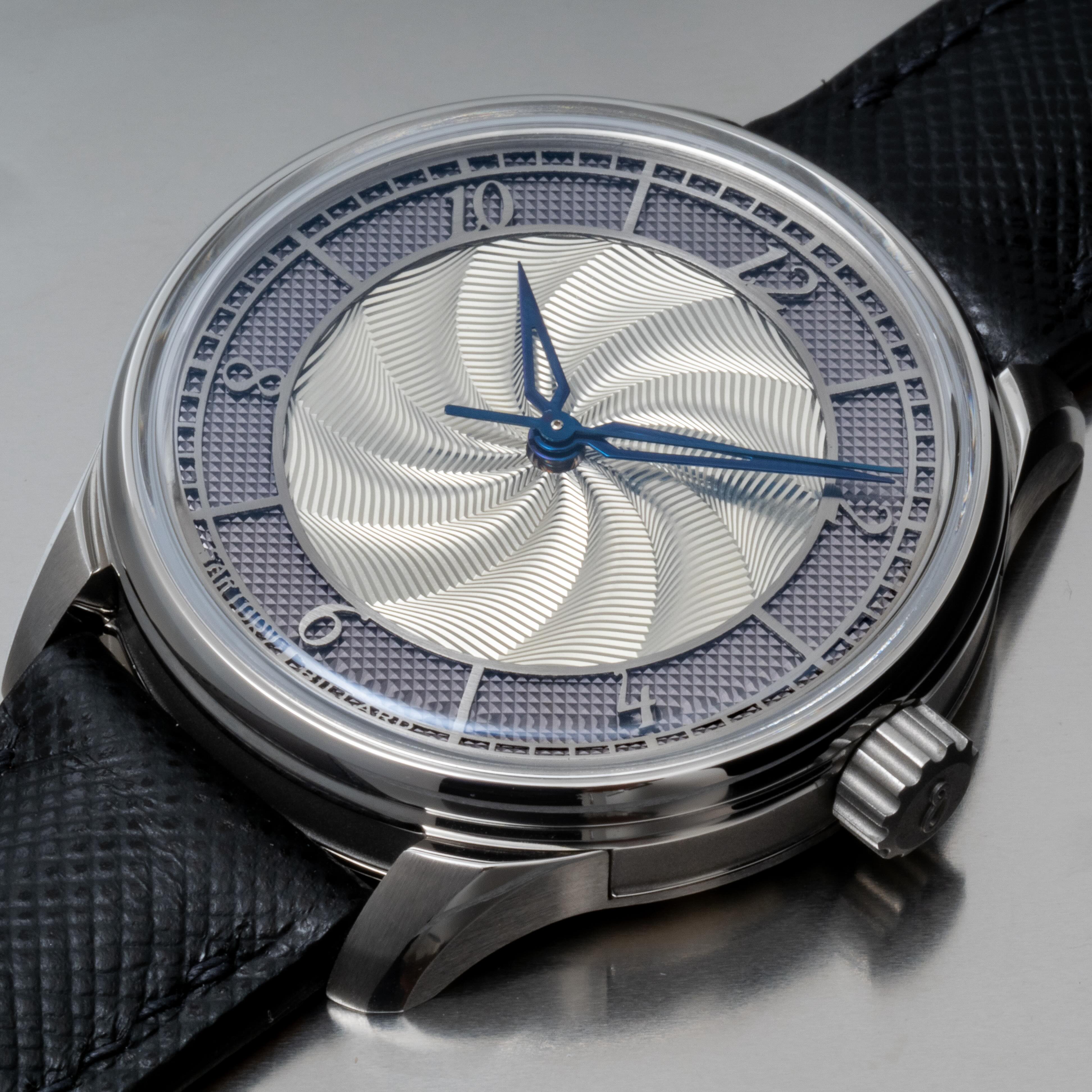
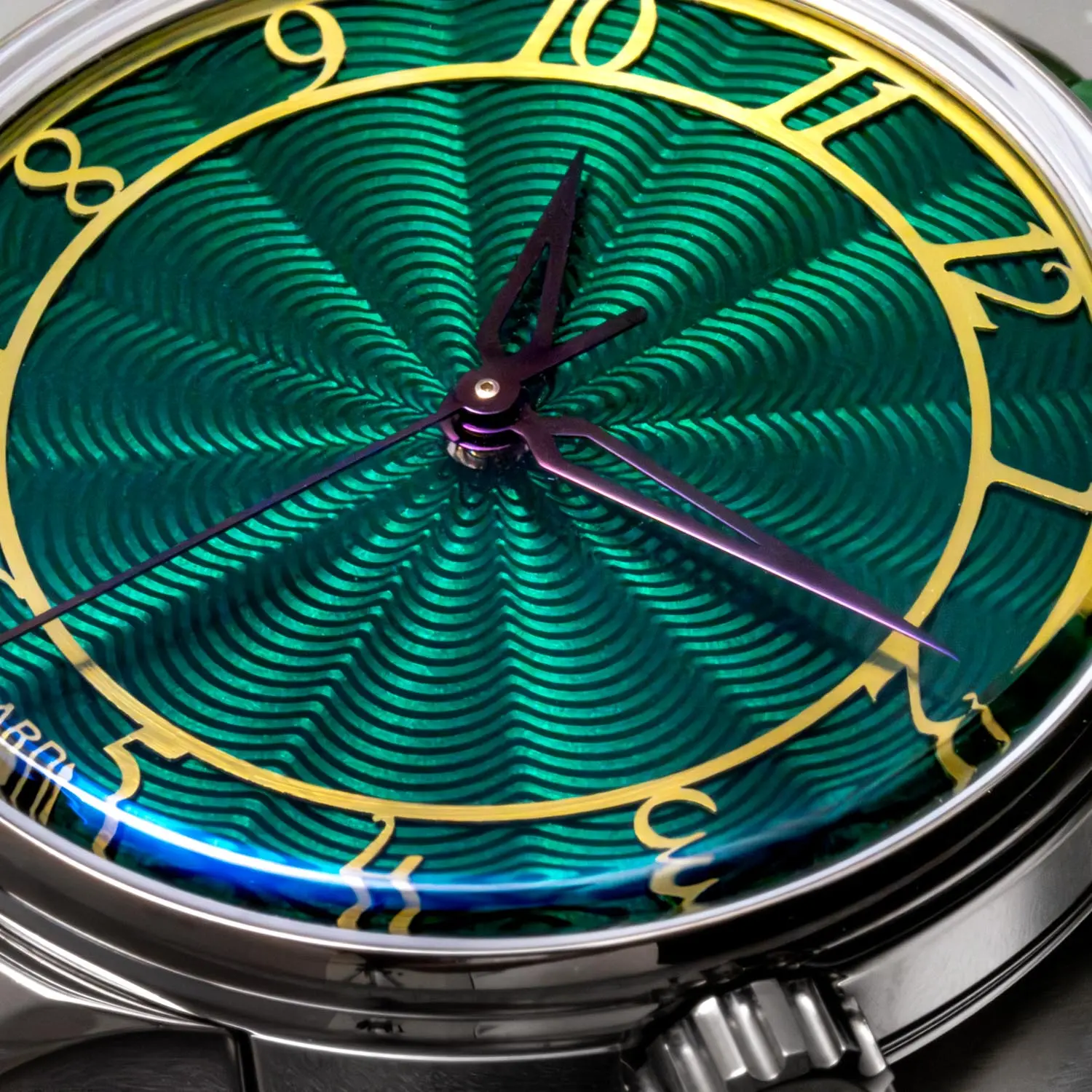
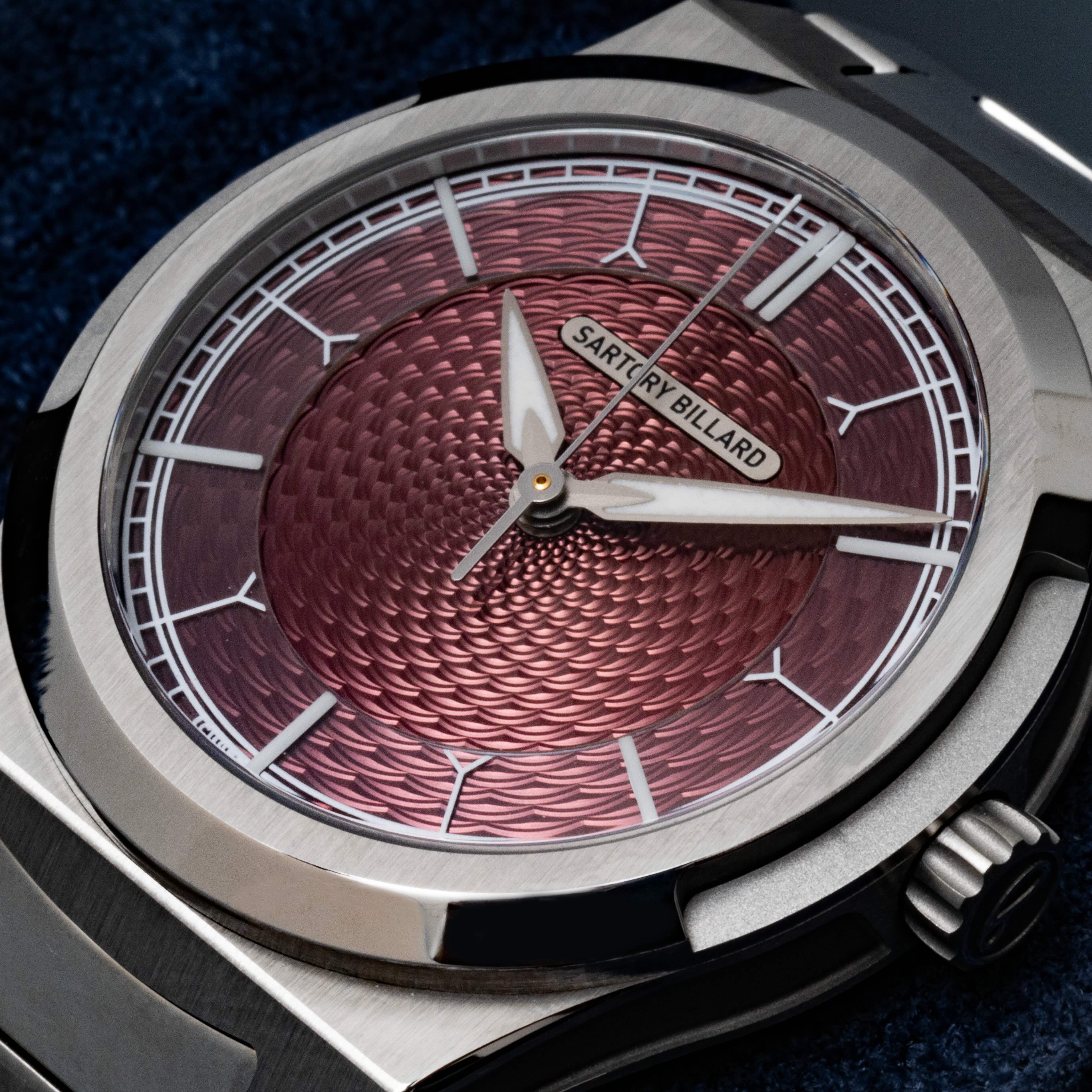
D. How to Distinguish Between the Two
While both methods can produce beautiful results, there are some telltale signs that can help you distinguish hand-engraved from machine-made guilloche:
☉ Pattern Regularity: Extremely perfect, absolutely consistent patterns are likely machine-made. Hand-engraved work will have subtle variations, even if they’re only visible under magnification.
☉ Depth Variation: Hand-engraved guilloche often has more noticeable variations in depth, creating a more dynamic play of light.
☉ Edge Quality: Machine-made guilloche typically has very clean, sharp edges. Hand-engraved work might have slightly softer edges due to the nature of the cutting process.
☉ Intersection Points: In complex patterns, the points where different sections meet can be revealing. Machine-made patterns will have perfect intersections, while hand-engraved work might show slight misalignments.
☉ Overall Character: Hand-engraved guilloche often has a certain warmth or personality that’s hard to quantify but noticeable to the trained eye.
It’s important to note that neither method is inherently superior. Many high-end brands use a combination of both techniques, leveraging the strengths of each. For instance, a brand might use CNC machining to create a base pattern and then refine it by hand, or use hand-engraving for limited edition pieces and CNC for their main collections.
Ultimately, the choice between hand-engraved and machine-made guilloche often comes down to the brand’s philosophy, the specific watch model, and the intended price point. For collectors, understanding these differences adds another layer of appreciation to the intricate world of guilloche craftsmanship.
VI. Guilloche Patterns and Designs
The world of guilloche is rich with a variety of patterns and designs, each with its own character and appeal. From traditional motifs that have stood the test of time to innovative modern interpretations, the range of guilloche patterns demonstrates the versatility and enduring appeal of this decorative technique.
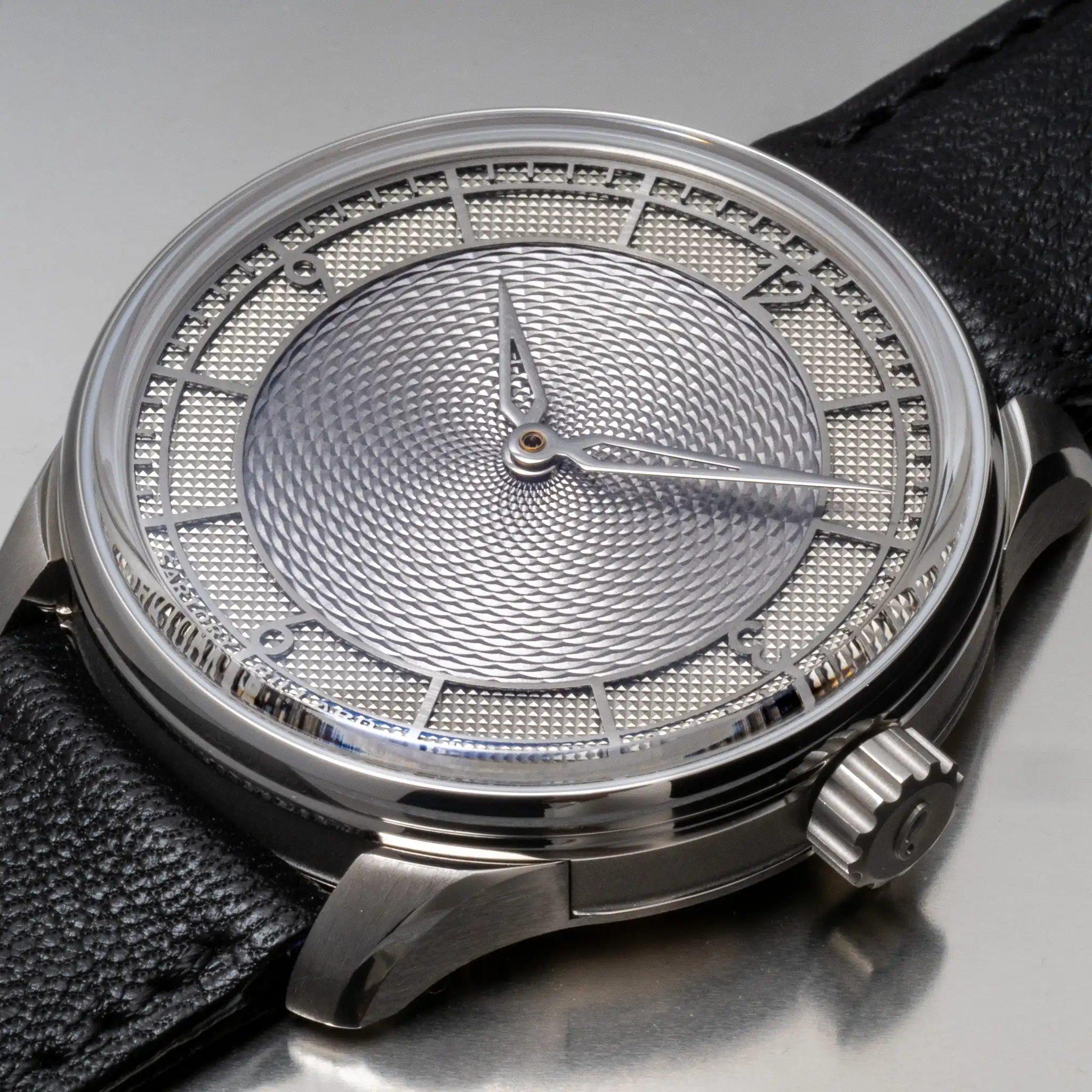
A. Classic Patterns
Many guilloche patterns have become classics in the world of watchmaking, instantly recognizable to enthusiasts:
☉ Clous de Paris (Hobnail): A pattern of small pyramidal shapes, creating a textured, almost shimmering effect.
☉ Barleycorn: Resembling grains of barley, this pattern features overlapping oval shapes.
☉ Sunburst: Radiating lines emanating from a central point, often used for the entire dial or within subdials.
☉ Wave: Undulating lines creating a sense of movement across the dial.
☉ Basketweave: Interlacing lines that create the appearance of a woven basket.
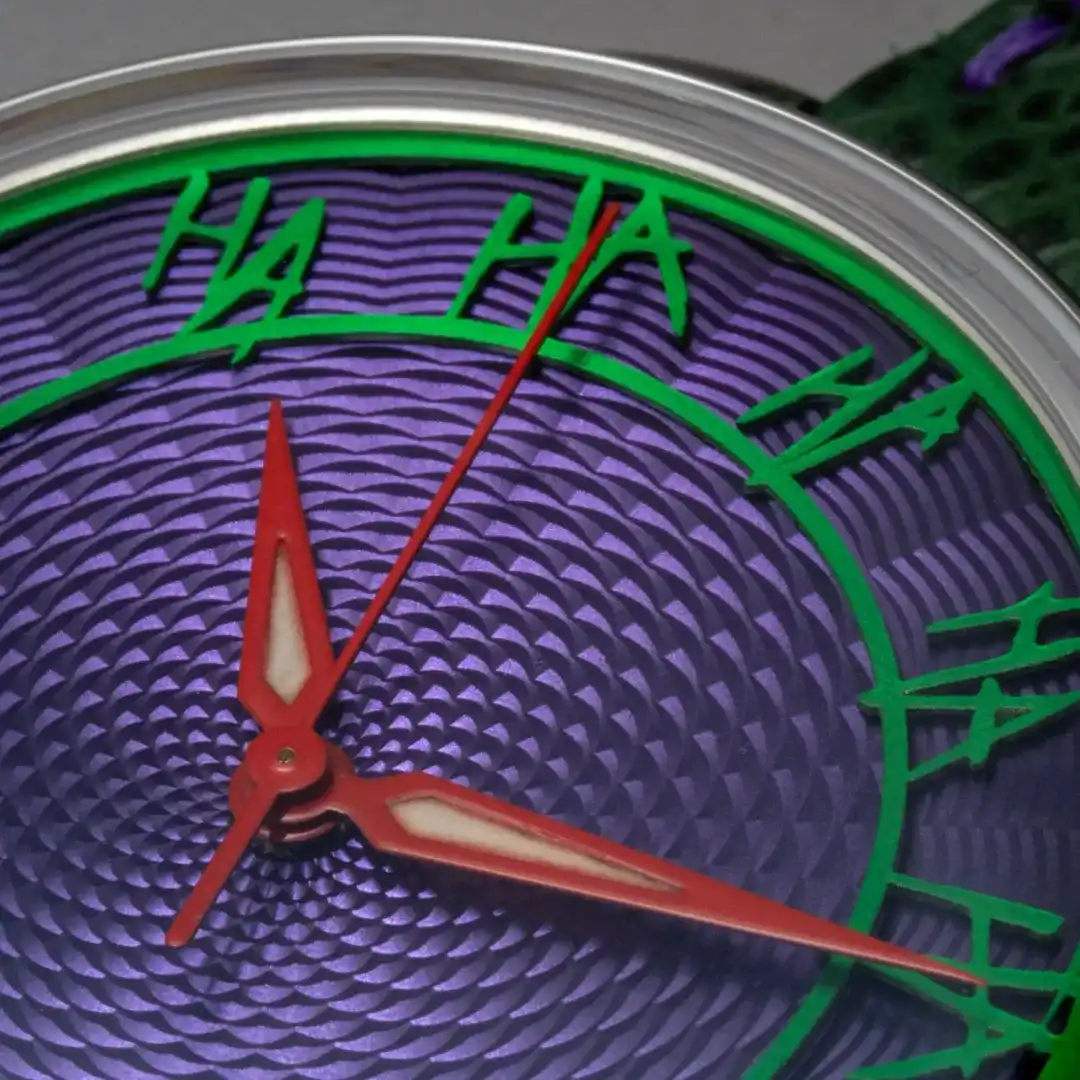
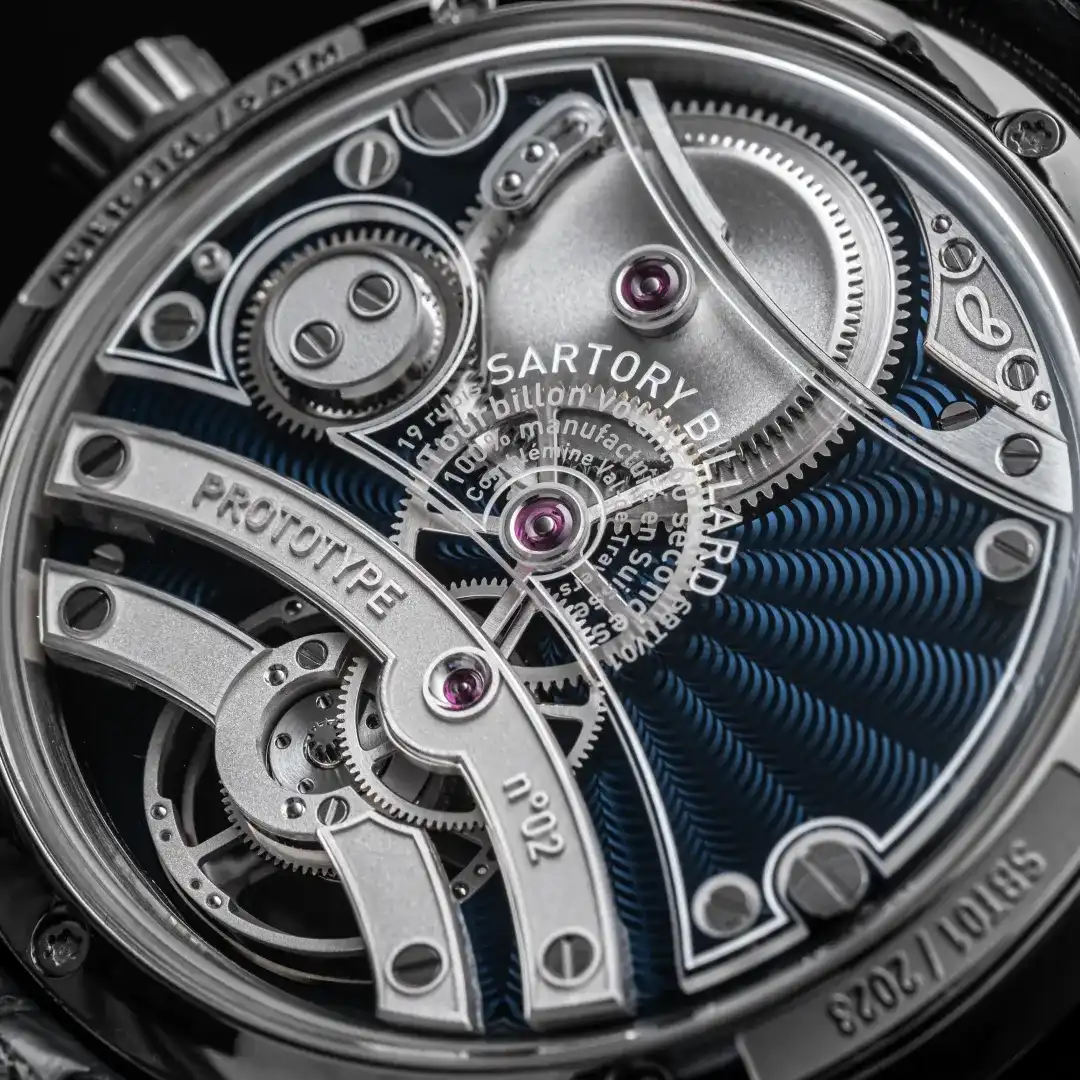
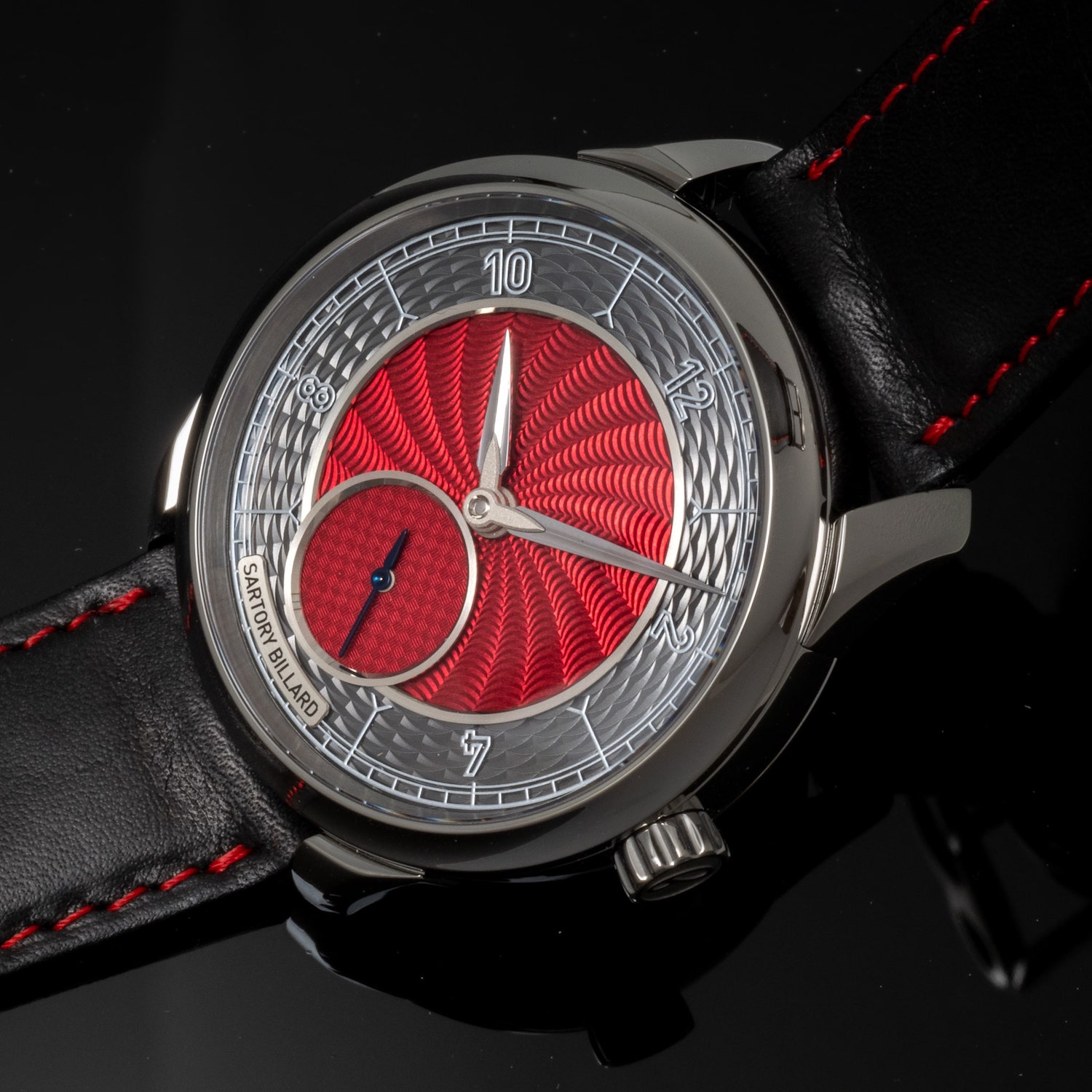
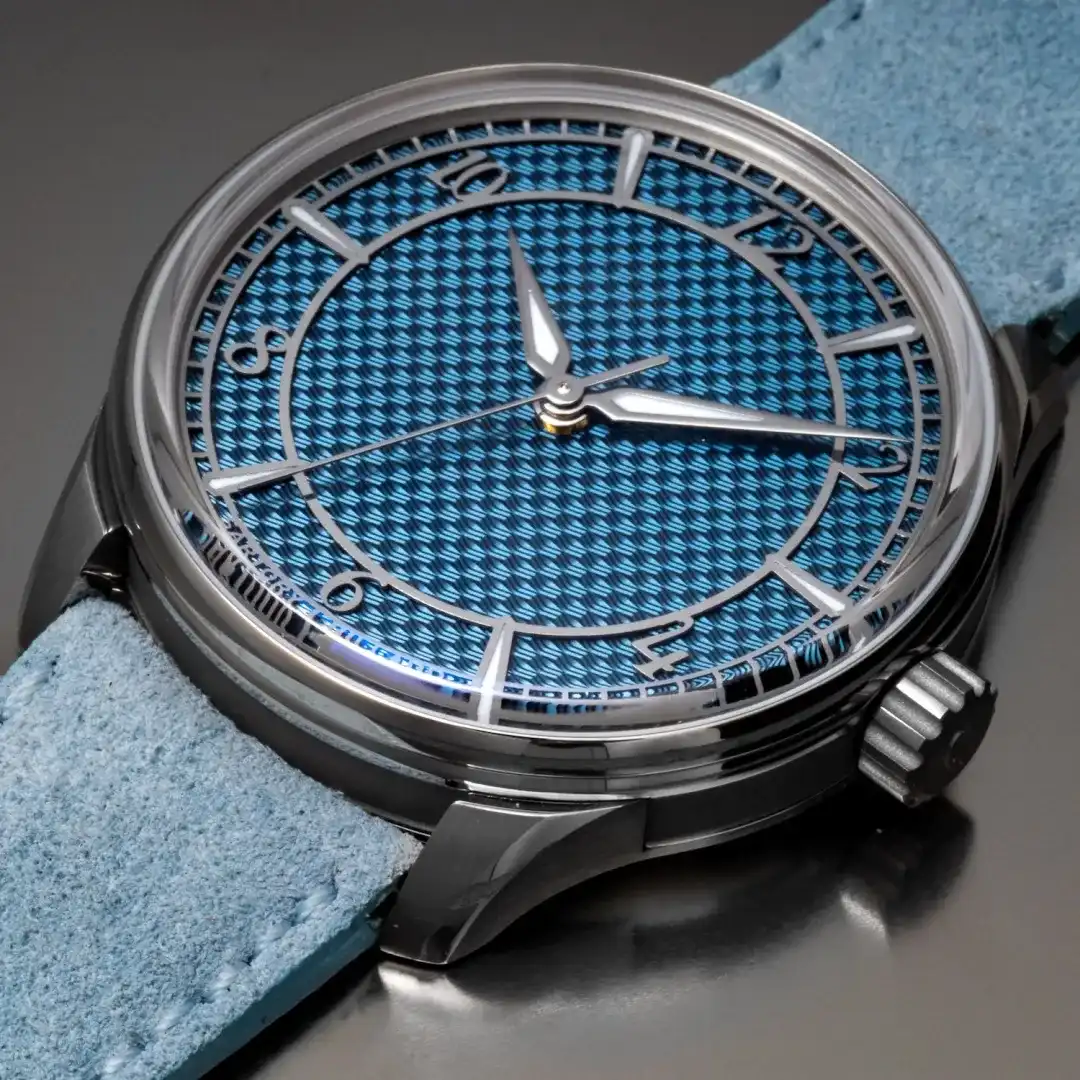
B. More examples

32 – La tornade

31 – Chevron

30 – Inverse 24 divisions

29 – Soleil vague 24 divisions

28 – Soleil levant

27 – Grand grain d’orge 60

26 – Grand grain d’orge

25 – Grand chevron

24 – Grain d’orge droit

23 – Petit panier

22 – Soleil vague 12 divisions

21 – Soleil vague 36 divisions

20 – Décor flèche

19 – Rotations inversée 36 divisions

18 – Rotations inversée 24 divisions

17 – Rotations inversée 12 divisions

16 – Soleil 24 divisions

15 – Décor bambou

14 – Clou triangle

13 – Soleil 36 divisions

12 – Décor losange

11 – Grand panier

10 – Soleil 12 divisions 3 bosses

09 – Soleil 12 divisions 2 bosses

08 – Soleil 12 divisions

07 – Petit grain d’orge

06 – Ecailles de poisson 36

05 – Décor agraphes

04 – Décor vagues

03 – Ecailles de poisson 24

02 – Clou moyen

01 – Grain d’orge horizontal
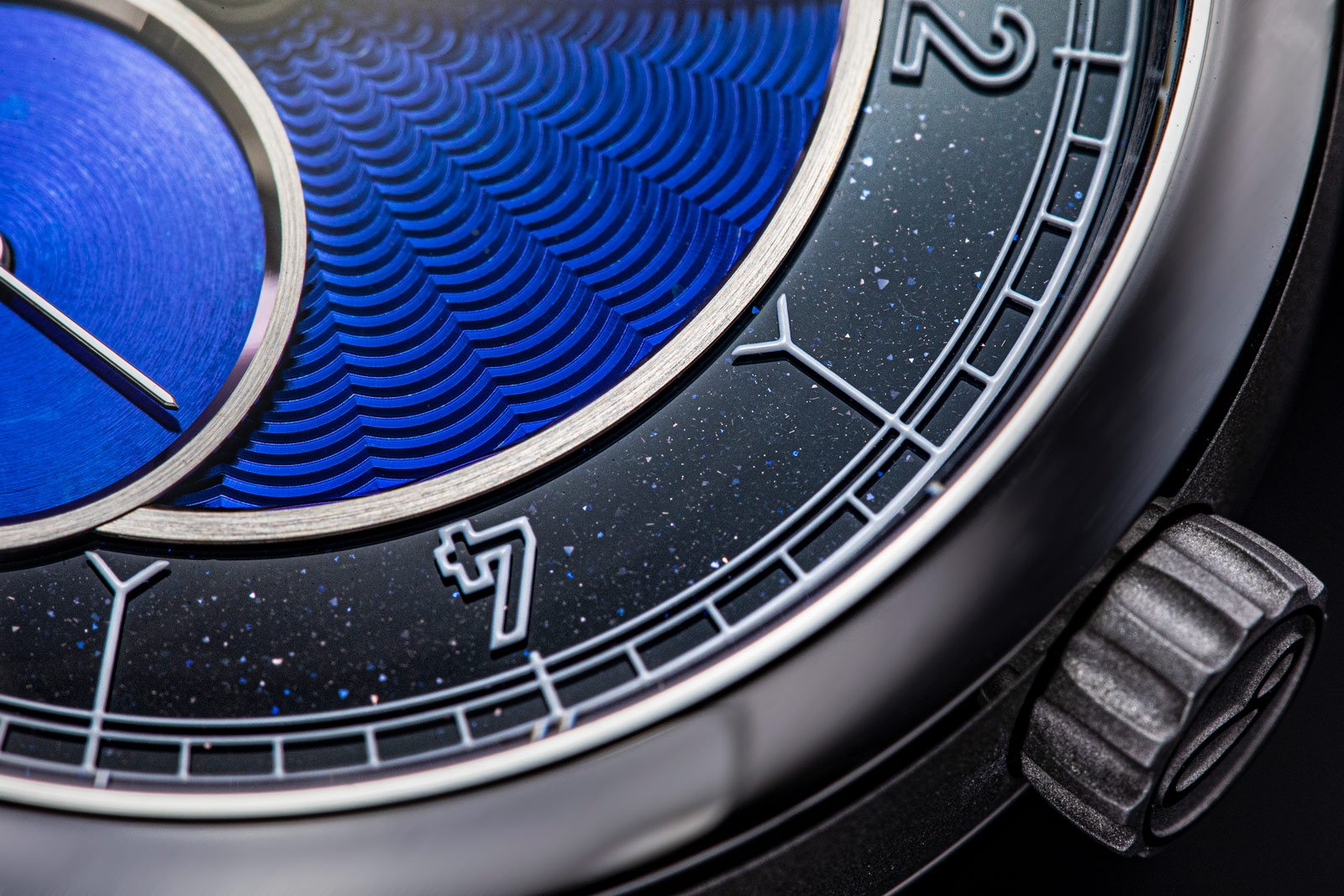
VII. Conclusion
The choice of guilloche pattern can significantly impact the character of a watch. Some patterns, like the Clous de Paris, lend a formal, traditional air, while others, like modern geometric designs, can give a watch a more contemporary feel. The scale of the pattern also plays a role – finer patterns tend to create a more subtle, elegant effect, while larger-scale designs make a bolder statement.
Moreover, the interplay between the guilloche pattern and other dial elements – such as applied indices, subdials, or complications – can create fascinating visual effects. Skilled designers use guilloche not just as decoration, but as an integral part of the dial composition, enhancing legibility and highlighting specific features of the watch.
As we continue to explore the world of guilloche, we’ll next look at some of the notable watchmakers who have made significant contributions to this art form, both historically and in the present day.